What it is and why it matters for the future of work for field workers.
Industry 4.0 is revolutionizing the infrastructure, industrial, and manufacturing sectors, allowing companies to achieve unprecedented levels of efficiency and innovation.
A key constituent in this change are frontline workers. Frontline workers are a crucial element in this transformation, and by embracing Industry 4.0 technologies, companies can empower their workers to work more efficiently, safely, and collaboratively, opening up new digital opportunities and gaining a competitive edge in the global market.
What is Industry 4.0?
Industry 4.0 — often referred to as the fourth industrial revolution – is characterized by the integration of digital technologies into the infrastructure, industrial, and manufacturing sectors. This new era is being driven by a variety of disruptive trends, including the increasing use of data and connectivity, advanced analytics, human-machine interaction, and improvements in robotics and automation.
One key aspect of Industry 4.0 is the rise of the Internet of Things (IoT), which refers to the network of connected devices and sensors that are being used to collect and transmit data in real time. This data can then be analyzed using advanced analytics tools to gain insights into operational performance, identify areas for improvement, and optimize production processes.
Another important trend in Industry 4.0 is the development of more advanced robotics and automation technologies. These technologies help companies automate a wide range of tasks and processes, including manufacturing, logistics, and supply chain management. This automation can significantly improve efficiency, productivity, and quality control, reduce costs, and minimize the risk of human error.
Industry 4.0 is also driving changes in the way that people interact with machines and technology. For example, the development of augmented reality (AR) and virtual reality (VR) is allowing workers to visualize and interact with data and digital models in new ways. This is helping to improve training and collaboration, as well as reducing the time and cost associated with design and prototyping.
How is Industry 4.0 transforming the work of frontline workers?
Industry 4.0 technologies and trends are having a profound impact on frontline workers across a range of industries, including manufacturing, construction, and utilities. These workers are using new tools and systems to perform their tasks more efficiently, safely, and collaboratively, leading to significant improvements in productivity, quality, and safety.
Robotics & Automation Revolutionize Manufacturing Frontline
In manufacturing, for example, frontline workers are using advanced robotics and automation technologies to perform a wide range of tasks, from assembling products to packing and shipping them.
By automating these tasks, frontline workers are able to spend less time on manual labor – which can be physically demanding and lead to injury – so they can focus on more complex and value-added activities such as quality control and process improvement.
Smart Tech Transforms Construction for Safety and Collaboration
Construction is another industry that is being transformed by Industry 4.0 technologies. Workers are using augmented reality (AR) and virtual reality (VR) technologies to visualize and plan construction projects, improving collaboration and reducing errors.
In addition, wearables such as smart helmets and safety vests are being used to monitor workers' health and safety, as well as their location and productivity. This data can then be used to optimize workflows and improve safety outcomes.
Transforming Utilities with Real-Time Mobile Collaboration and Predictive Maintenance
In Utilities, workers are using mobile devices and cloud-based software to access information and collaborate with colleagues in real-time. This allows them to respond to customer requests and resolve issues more efficiently, reducing downtime and improving customer satisfaction. In addition, utilities companies are transforming their field operations by adopting new scheduling technologies that are helping field personnel reduce unproductive drive time and mileage by 30%.
Finally, predictive maintenance technologies are being used to monitor equipment performance and predict when maintenance is needed, reducing the risk of equipment failure and improving overall reliability.
Navigating the Opportunities and Challenges of Industry 4.0 for Telecom
Industry 4.0 brings a wealth of potential benefits and challenges for frontline workers in the telecom field service industry.
Improved Productivity
Telecom workers can benefit from improved productivity, as smart machines and data analytics streamline operations and reduce errors. For example, with the help of advanced technologies like the Internet of Things (IoT), Artificial Intelligence (AI), and Augmented Reality (AR), field workers can quickly and accurately diagnose problems, streamline maintenance and repair tasks, and reduce the time and cost of service visits.
Higher Safety
The adoption of advanced technologies and automation can also promote worker safety by reducing the need for workers to perform manual work in hazardous environments.
Increased Job Satisfaction
Frontline workers may also experience increased job satisfaction due to a greater sense of accomplishment on the job. For example, armed with real-time data and insights, workers can better serve their customers. In addition, the elimination of mundane tasks via automation allows more focus on value-added activities. And finally, with the time savings afforded by automation and other technologies, frontline workers can acquire new skills and engage in more challenging and interesting work.
Privacy Concerns
Industry 4.0 is not without its concerns. As connected devices and systems gather vast amounts of personal data, and companies adopt AI, concerns about privacy and data security have become more pressing.
Staying Relevant
While Industry 4.0 presents opportunities for telecom field service workers, there are also concerns that it may displace certain jobs and exacerbate skill gaps. Careful consideration of these challenges is necessary to ensure a smooth transition to the new technological paradigm. Some workers may find themselves out of work or in need of new training to stay relevant.
As Industry 4.0 continues to evolve, it will be important to carefully consider these benefits and challenges and work to address them in a way that maximizes the positive impact for both workers and organizations.
How can frontline workers prepare for Industry 4.0?
As the majority of workers worldwide are deskless, it is important to address the issue of Technology Equity to enhance the lives and productivity of these workers.
Frontline workers can stay ahead of the curve and thrive in the rapidly evolving Industry 4.0 landscape by taking several steps.
- First, they should embrace a continuous learning mindset and stay up-to-date on emerging technologies and industry trends. This can be done through attending training sessions, participating in online courses or workshops, or pursuing relevant certifications.
- Second, workers should focus on developing digital literacy and proficiency, including basic computer skills and familiarity with data analysis tools.
- Third, workers should be open to collaboration and teamwork, as Industry 4.0 emphasizes cross-functional and interdisciplinary work.
- Finally, workers should be proactive in identifying opportunities to apply new technologies to improve processes and workflows in their work environment.
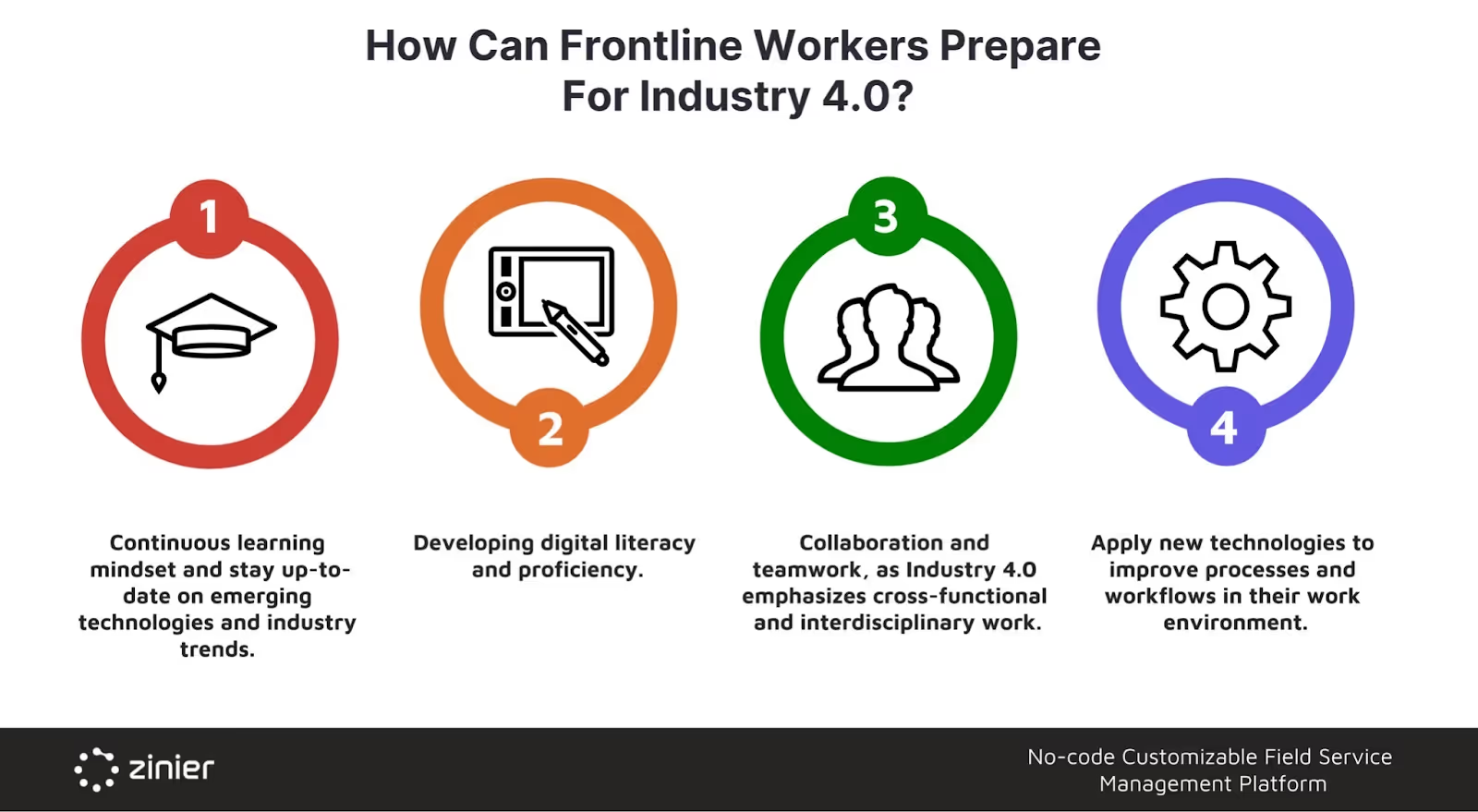
By taking these steps, frontline workers can position themselves for success in the era of Industry 4.0.
How can Telecom companies prepare for Industry 4.0?
To truly stand out from the competition, many companies are placing greater emphasis on value-added services and the quality of their service delivery.
- Putting Customer Service First
Providing access to broadband is still necessary, but is no longer sufficient for companies aiming to thrive in the fast-paced market for fiber-to-the-premises and other competitive offerings. To truly stand out from the competition, many companies are placing greater emphasis on value-added services and the quality of their service delivery.
- Getting the most out-of-field teams
With the ongoing labor and skill shortages, Telecom operators need to ensure they are getting the most out of their existing field teams and automating processes as much as possible to free dispatchers to focus on solving customer problems. Companies can increase their efficiency and productivity by automating and optimizing technician scheduling based on factors like utilization, travel, experience, capacity, and availability.
- Managing and Automating Resource Planning
But scheduling has its limitations – if you don’t have the resources to meet demand, it won’t matter how powerful your scheduler algorithm is. And because capacity and demand are constantly changing, you need a tool that allows you to adjust and optimize your workforce accordingly.
- Boosting Field Team Productivity with Effective Strategies
Remote Assistance and other real-time collaboration tools are aimed at improving productivity. When combined with effective scheduling and a customer-first approach, they can equip field teams with the necessary support and knowledge to succeed.
Getting Started
By embracing Industry 4.0 disruptive technologies, companies can unlock new levels of efficiency, productivity, and innovation, leading to a competitive advantage in the global marketplace.
For telecom frontline workers, Industry 4.0 brings both potential benefits and challenges. Improved productivity and safety are among the benefits. Smart machines and data analytics can streamline operations, reduce errors, and automate dangerous or repetitive tasks. Telecom workers can access real-time data and insights to better serve customers and acquire new skills and engage in more challenging work.
Telecom companies who are new to implementing Field Service management in their service operations or considering it can benefit from adopting best practices that have already been tested by industry leaders.
Here are some recommended actions:
- Instead of searching for a temporary solution to meet your immediate needs, it is advisable to invest in an end-to-end platform that can support your long-term growth plans.
- While it's important to have a solution with an efficient scheduling algorithm, it's also crucial to consider the experiences of both field engineering employees and end customers. For field engineers, it's essential to enable them to complete the job correctly on their first visit and avoid multiple visits. For customers, it's beneficial to minimize the need for phone calls by providing digital tools for communication with the company and setting clear expectations.
- ESG (Environmental, Social, and Governance) is becoming increasingly important in the field service management industry. In the telecom industry, where sustainability is a top concern, incorporating ESG principles into field service management can help companies meet their environmental targets and increase customer trust and loyalty.
To know what the future might look like for your frontline workers, I invite you to meet with our team who has a deep understanding of the world of deskless and frontline workers, which enables us to orchestrate workflows that facilitate the development of a smart, connected, sustainable world.