The Parts & Inventory Advantage
Zinier’s Parts & Inventory product enables field service operations to keep track of parts and material inventory across warehouses and trucks, and ensures that technicians have the right parts and materials they need to complete their tasks.
Our latest release introduces a significant improvement to the way parts and inventory are managed, empowering users to track and manage inventory at the unit level.
Taming Inefficiency Through Inventory
You know the expression that a chain is only as strong as its weakest link? For many field service operations, inventory management turns out to be that weakest link.
According to research by McKinsey, 40% of a typical field technician's workday is spent on unproductive activities. And there's a good chance that inventory issues account for a good part of that wasted time. And those inventory glitches can easily cascade into all kinds of problems – driving down first-time fix rates, pushing up repeat truck rolls, and hurting your SLA and customer satisfaction metrics. And of course all of those metrics wind up affecting your company's bottom line.
Here are some of the common challenges that often arise when managing parts and inventory:
Lack of visibility
Lack of visibility into each stock location and its inventory stock is one of the biggest causes of inefficiencies, leading to increased operational costs.
Poor planning
Just getting the right technician to the right location at the right time may not be enough – they still can't address the problem when they don't have the parts that are needed.
Managing the unexpected
When the unexpected happens in the field, how do you get parts to techs so they can be unblocked and prevent a second truck roll?
Here’s a preview of some of the key ways that Zinier’s new Parts & Inventory functionality addresses these problems.
Unit-level Inventory Tracking
In speaking with customers who were using the Zinier platform to manage parts and inventory, one request kept surfacing: how can we track parts and inventory at the unit level?
Not all field service organizations need to keep track of individual parts – for some, tracking quantities is enough. But for those that want to be able to track the entire lifecycle of an individual part – from warehouse to truck to customer – we often found ourselves using our platform to develop a customized solution.
That capability to track parts at the unit-level now comes out-of-the-box. You’ll see this capability in several places:
Stock locations: Specify which box number the parts belongs to when adding inventory
When adding a catalog item to a stock location, backoffice users can specify a box number for each individual part added. This helps inventory managers know the exact location of a specific part when it’s stocked in a warehouse.
Stock locations: Add individual parts (and serial numbers) when adding inventory
When adding a catalog item to a stock location, backoffice users can specify the serial number of each individual part added. This enables inventory managers to track the lifecycle of individual parts.
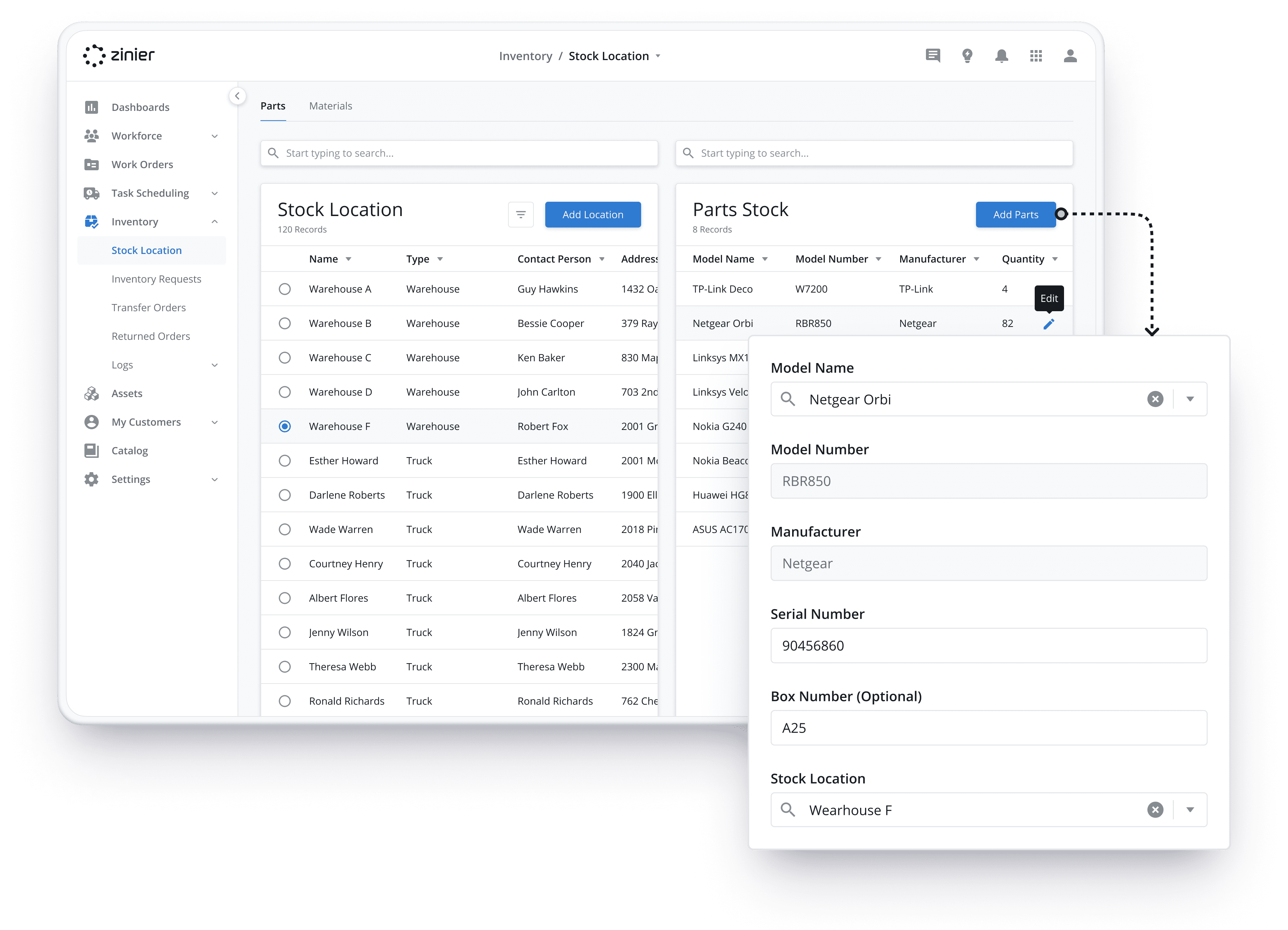
Transfer orders at the unit-level
Inventory requests are fulfilled by creating transfer orders that allow backoffice users to transfer parts and materials among different stock locations. Together, inventory requests and transfer orders ensure that technicians have the right parts and materials they need to complete their tasks.
Users can now select the serial number of parts to be reserved when creating a new transfer order and can select the serial number of parts received when fulfilling a transfer order. The system will also offer intelligent suggestions about which warehouse to source the parts from based on the parts required in the transfer order.
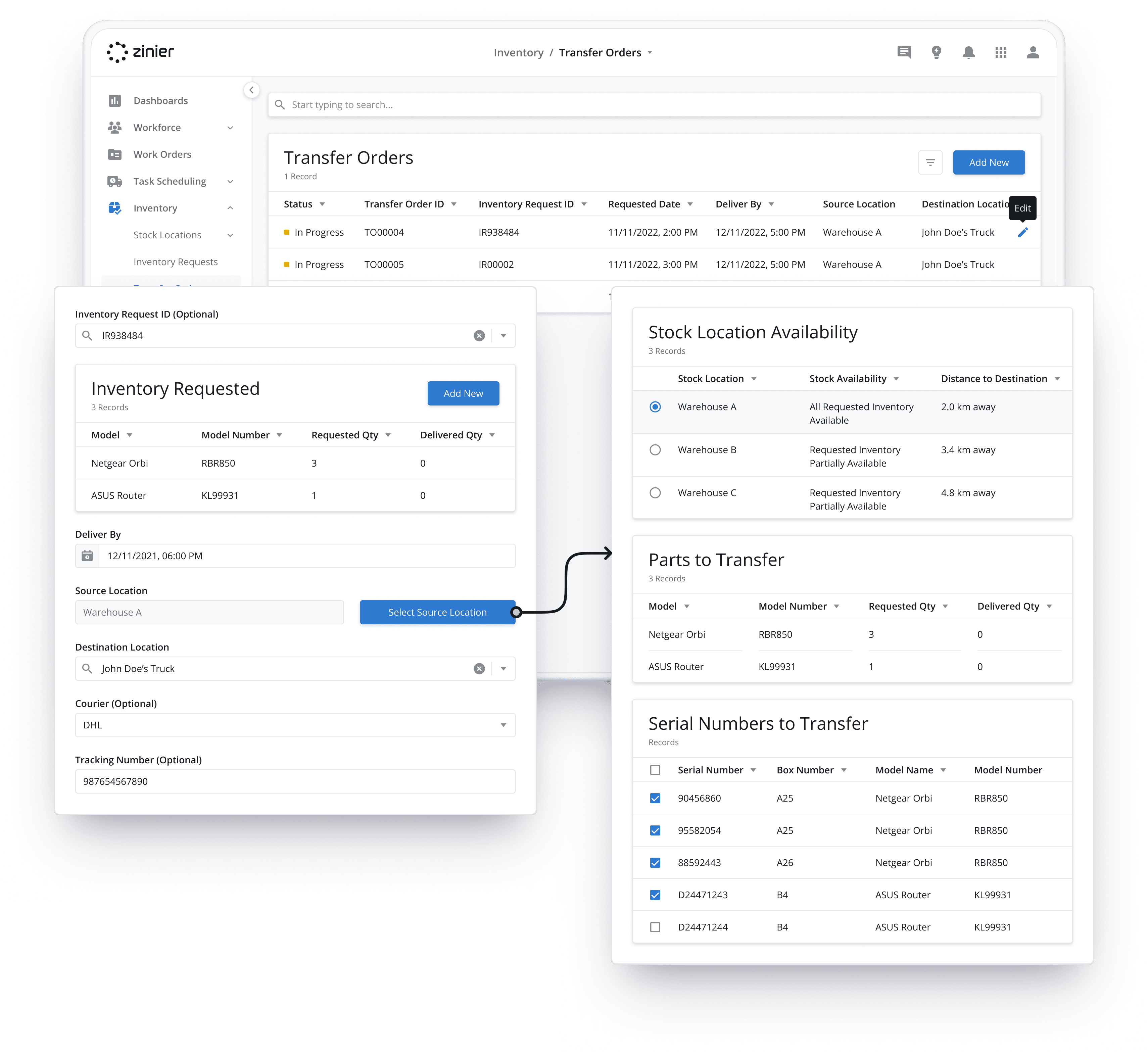
Return orders at the unit level
Return Orders allow backoffice users to accept any parts or materials returned by technicians after the completion of their tasks. The returned parts might be new and unused parts to be restocked or faulty parts that need to be discarded. With this release, users can now select the specific serial number of parts returned when fulfilling a return order.
Field experience: Request and receive parts at the unit level
Technicians in the field can also specify the serial numbers of parts they’ve received as part of the mobile inventory experience.
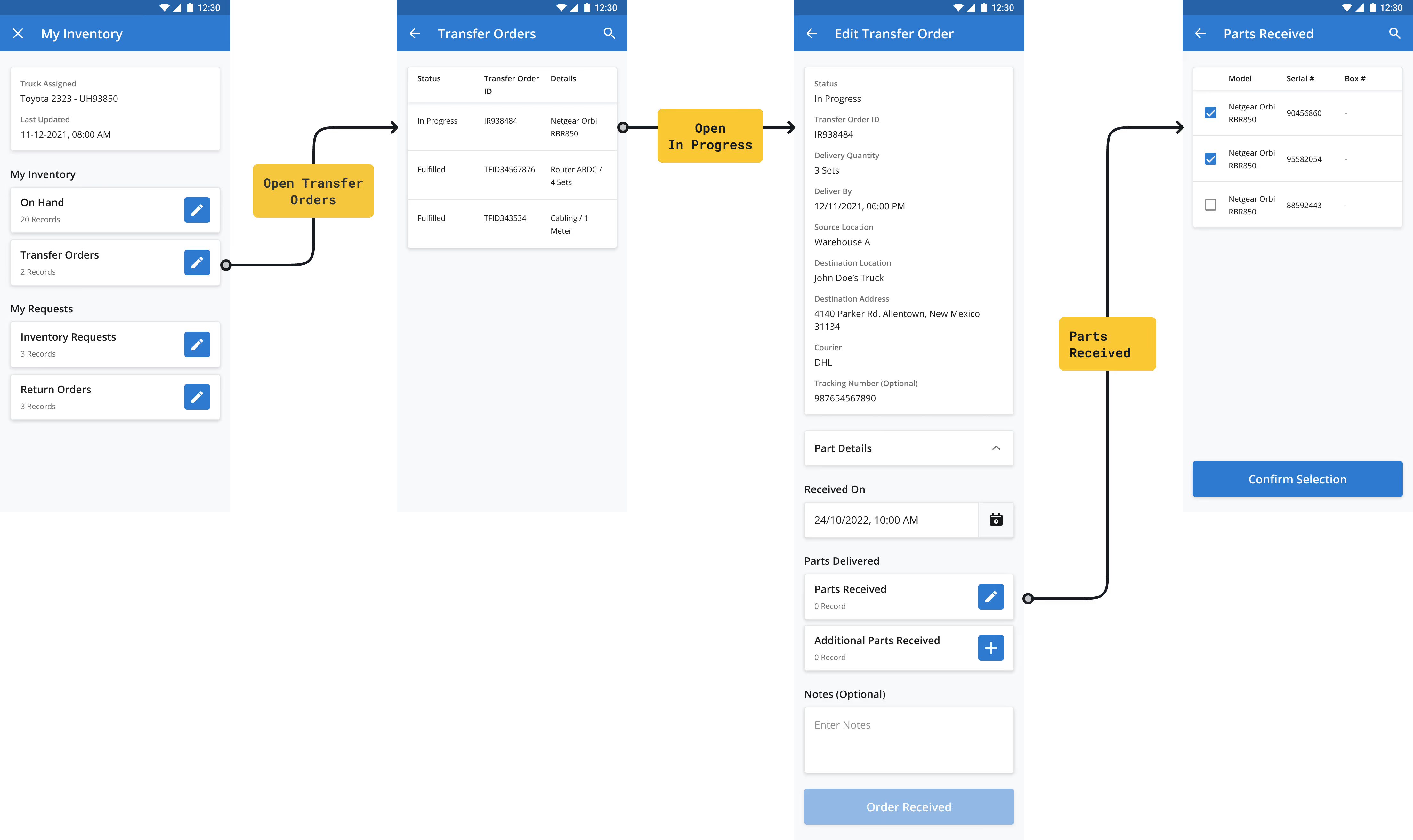
Additional UI/UX Enhancements
Parts Transfer Logs
In addition to unit-level tracking, we’ve also introduced a new Parts Transfer Logs module. Parts Transfer Logs gives backoffice users a singular view to see all inventory that may have gone missing or incorrectly delivered – providing another means to track the full lifecycle of individual parts.
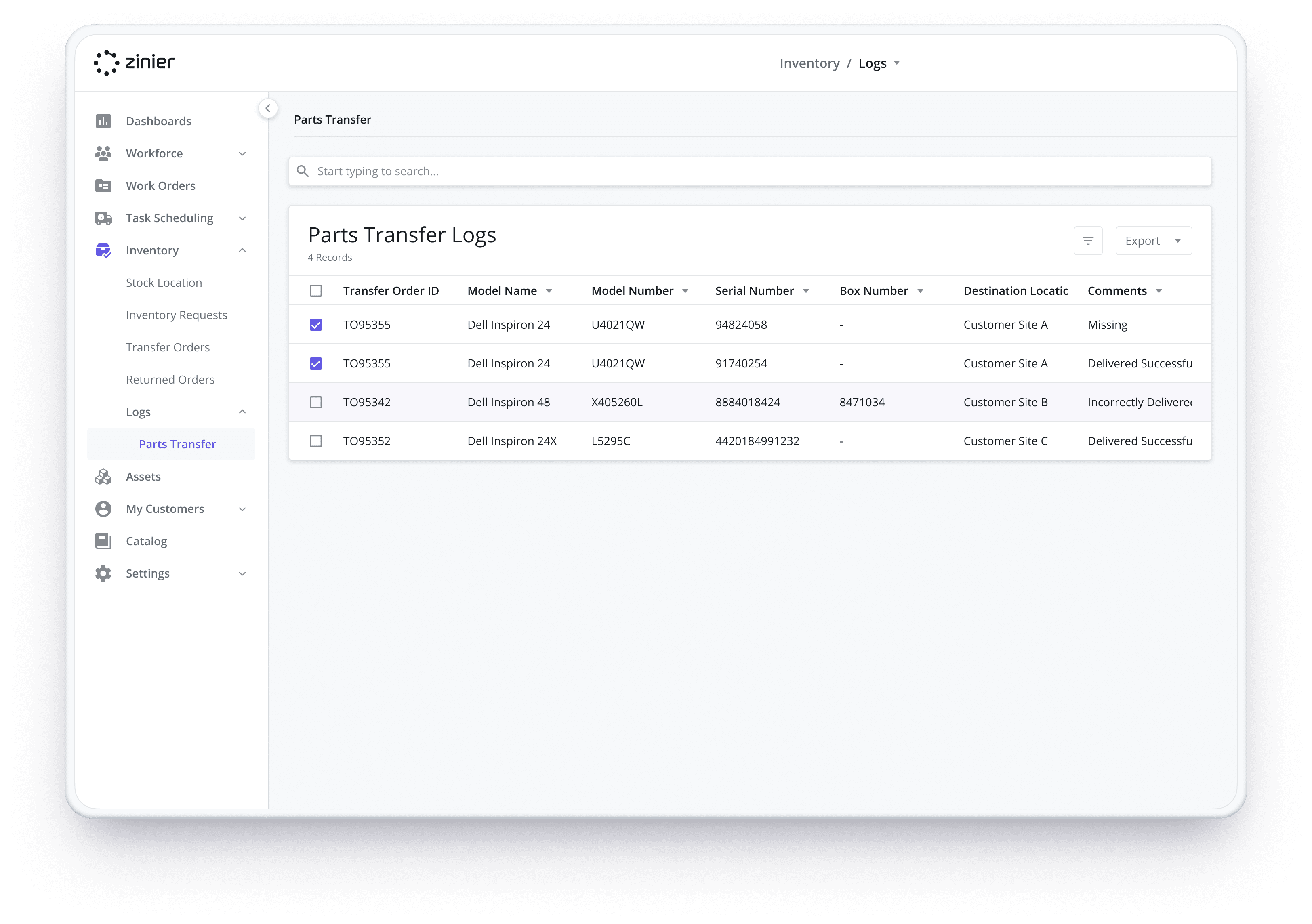
Adding multiple items to a single inventory request or transfer order
Last but not least, inventory managers can now add multiple items (different catalog items) to a single inventory request or transfer order. Prior to this enhancement, users were required to create a separate transfer order/request for each catalog item, which could get cumbersome when multiple different items were required.
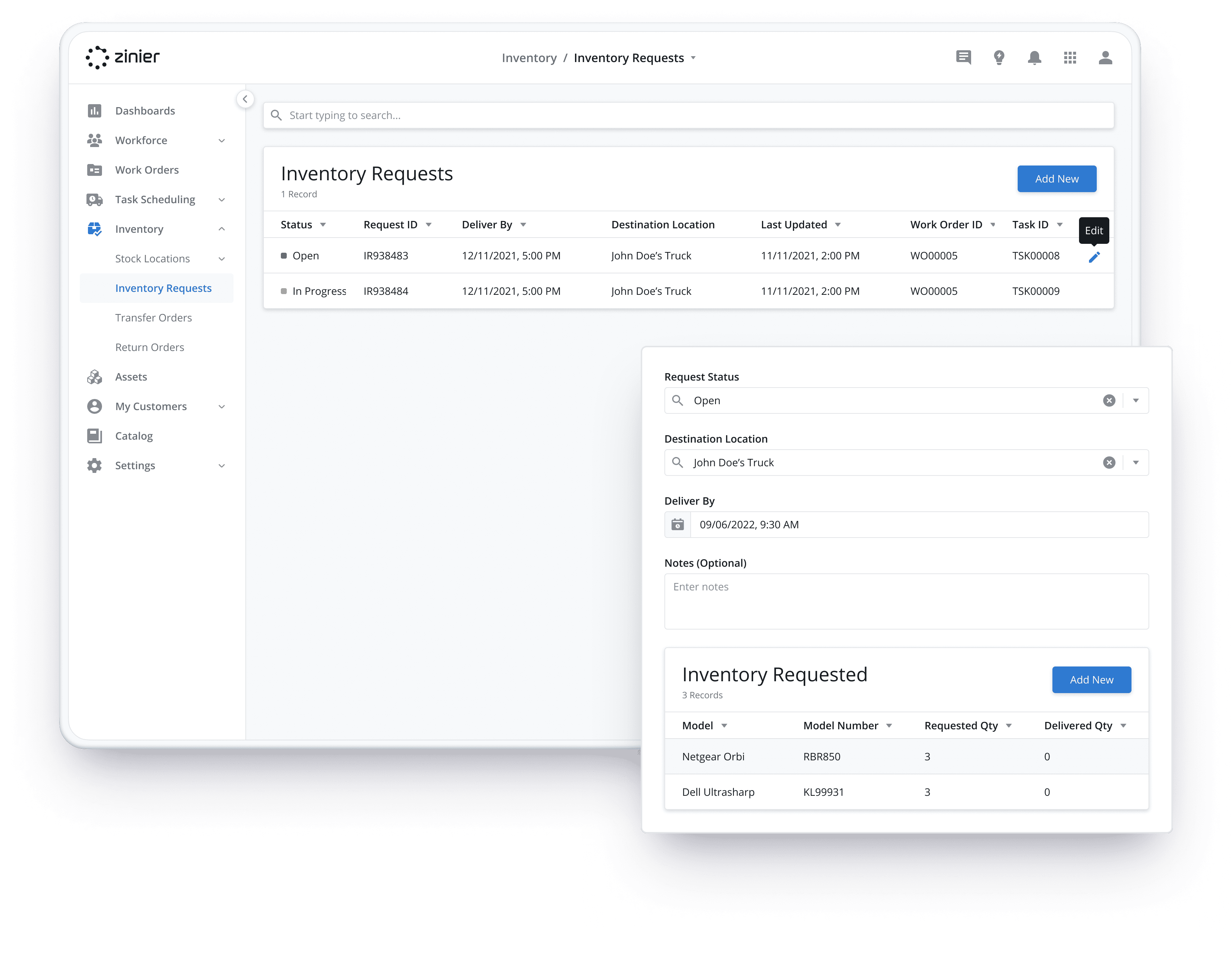
Want to see the Zinier platform in action? Schedule a demo today!